Preventing repainting failures caused by hydrophobic substances that hinder localised paint adhesion to the substrate is a challenging task. Optimiza has invested years of research into developing one or more relatively rapid identification methods for these substances (24-48 hours).
Following extensive research in projects and the laboratory, Optimiza has achieved a significant breakthrough in the yachting industry with the successful development of the Ceramic Removal Test (CRT). This innovative method addresses the challenges associated with thin ceramic coatings, which have become a valuable alternative for enhancing and preserving topcoat finishes, especially in critical areas such as the hull and superstructure.
The primary advantage of these coatings lies in their ability to extend the lifespan of the topcoat through periodic polishing and application treatments, significantly prolonging the repainting interval. However, incomplete removal of these coatings during repainting can lead to costly defects, such as craters, underscoring the importance of the CRT.
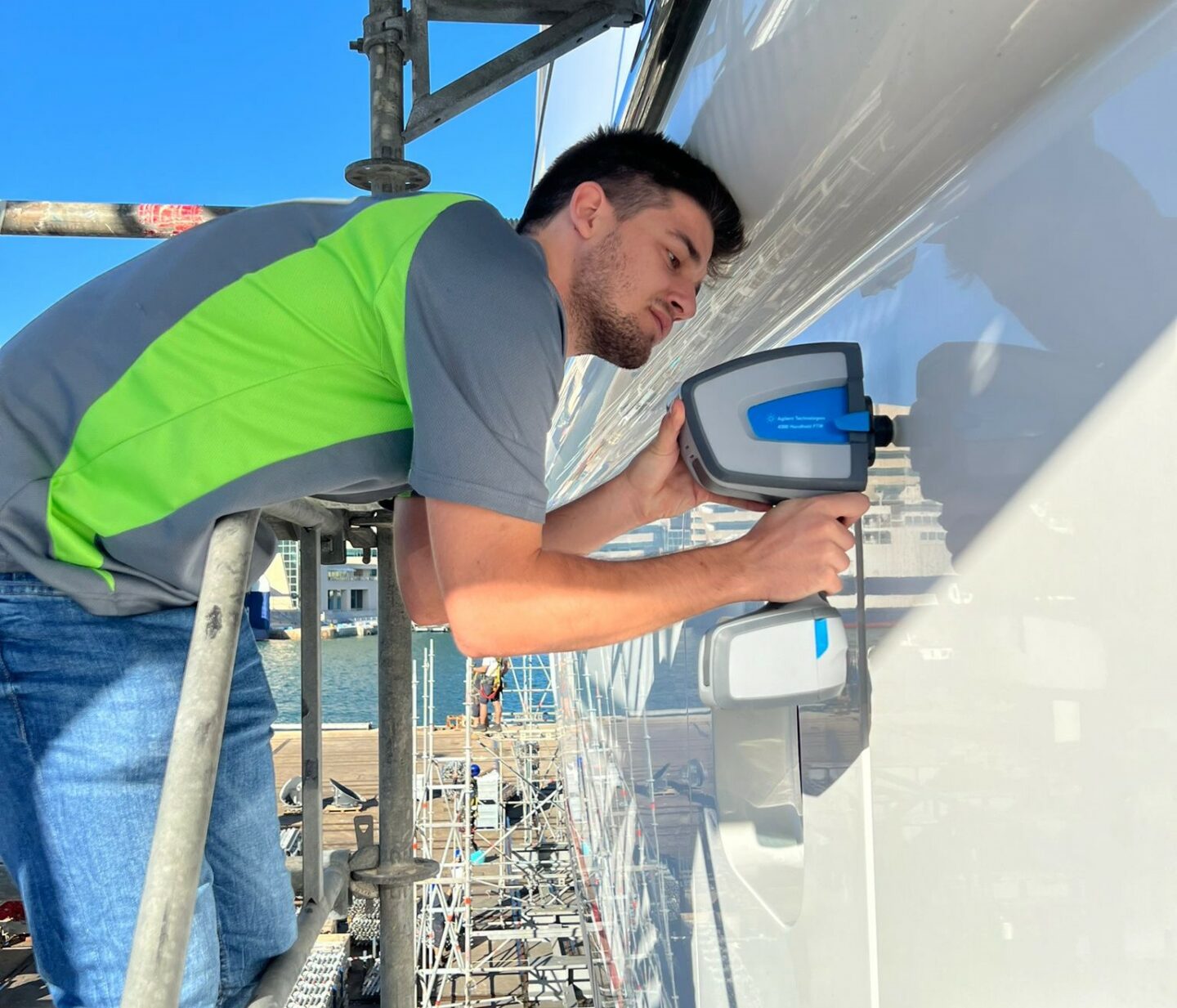
Ceramic coatings are increasingly used to protect surfaces, but their wide variety of compounds based on silicon, aluminium, zirconium, and titanium make general and effective treatment difficult. Moreover, the different types of chemical bonds present in these coatings make their removal from the surface and analysis technically complex but feasible using the appropriate professional team and resources.
The above-mentioned complexity of ceramic coatings, which may include a variety of compounds and chemical bonds, poses additional challenges for their identification and treatment. These coatings may contain Si-O-Si, Si-B, Si-C, Si-N, and mixed bonds, which influence their behaviour and properties. The interaction between the ceramic coating and the substrate can generate interference in spectroscopic analyses (FT-IR), making precise interpretation of results difficult.
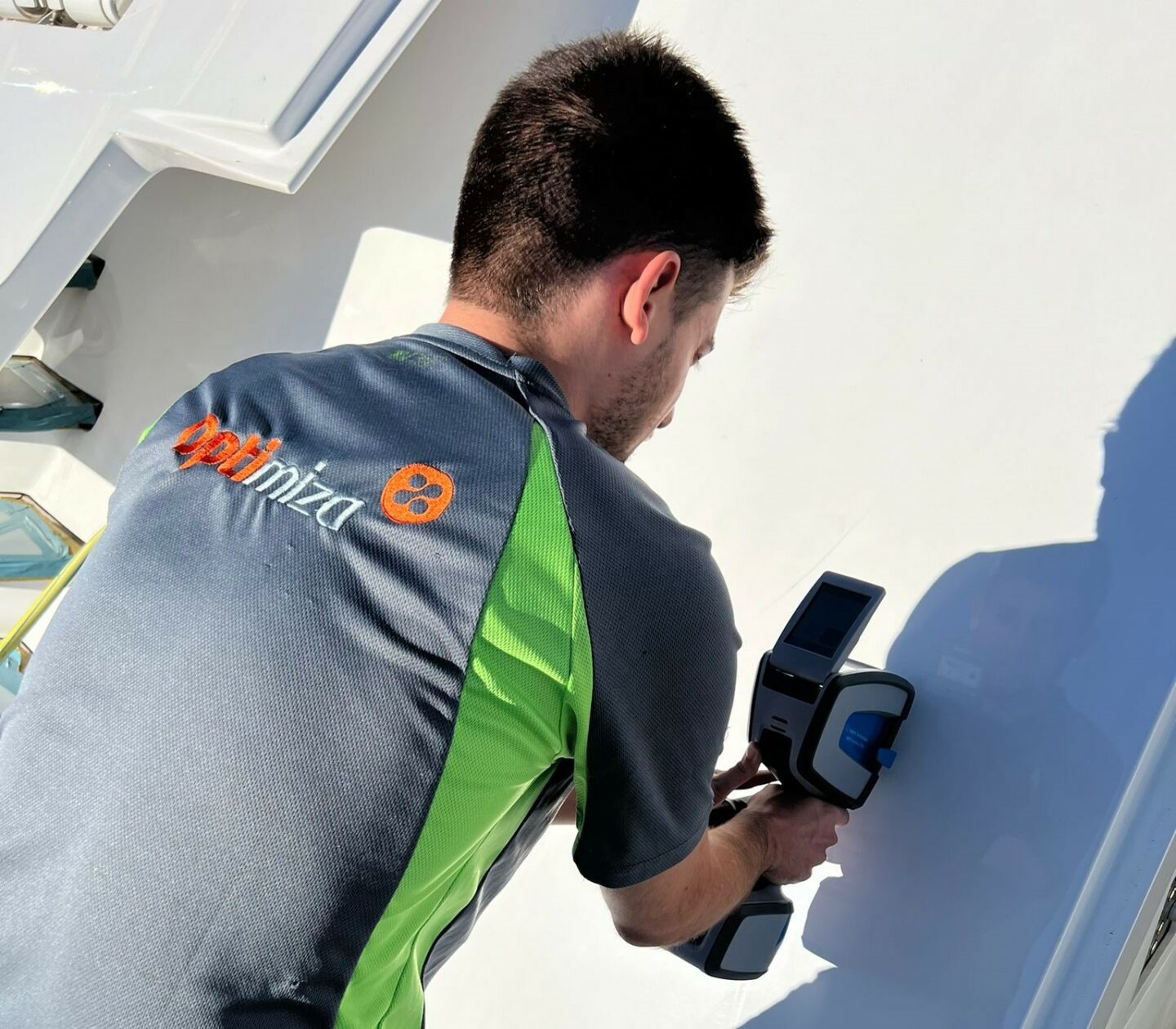
It is also important to consider the type of substrate, as it can generate interference in the coating signals and create false positives. Hydroxyl, carbonyl, and urethane bonds are the most common and can affect surface hydrophobicity, leading to defects in paint application. Additionally, measuring thin layers of coatings without substrate signals requires skill in the use of surface analyzers such as the FT-IR-ATR technique. This instrument, which can be portable or benchtop in the laboratory, can collect surface data, but it must be subsequently analysed and interpreted by a polymer expert, as the bands emitted by the instrument are not sufficient to determine if a surface has ceramic compounds or other compounds or contaminants that may generate differences in surface tension leading to defects such as craters or dimples in the topcoat application phase.
Distinguishing functional groups of old polyurethane from ceramic residues requires years of research, and ensuring whether a surface is free of these components must be done very carefully based on verified facts. It is not only Polydimethylsiloxane (PDMS) that can cause defects during painting; other components and additives from different ceramics and polymers or airborne contaminants can also cause these defects. See below in the picture a sample applied with a ceramic with a specific type of PDMS and a sample with no PDMS but with components that affect the surface tension when a coating is applied. Not all ceramics or polymers have the same composition, and the compounds that generate hydrophobicity leading to painting defects can be different and in different proportions in their formula. Therefore, it is important to consider these factors to avoid repainting defects.
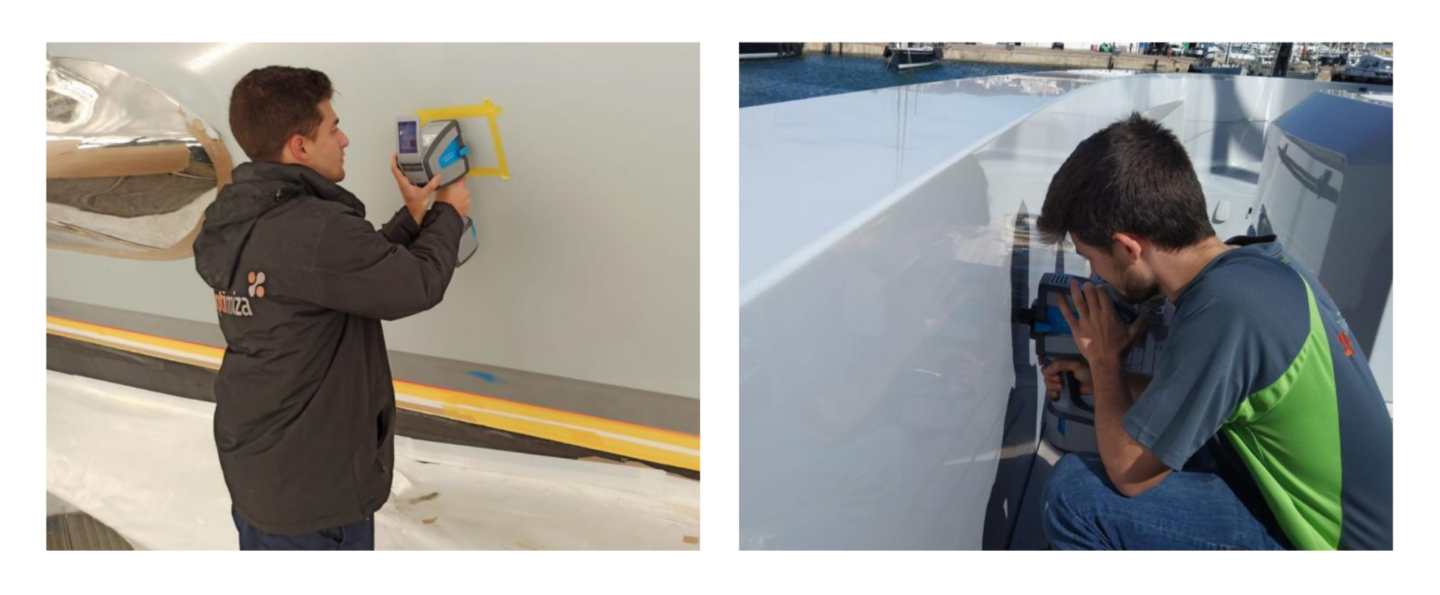
To address these challenges, Optimiza has conducted extensive research. The initial part of this research was carried out in collaboration with Cerashield (a market-leading company in the supply and application of ceramic coatings) with the first studies on the behaviour, characterization, and qualification of the removal method of their product.
“At Optimiza, we are grateful to Cerashield for their commitment to R&D and for conducting such a detailed study with us and with GYG for entrusting our laboratory with a significant number of ceramic compound analyses and failure prevention tasks which facilitated subsequent progress in our own research and they made a big contribution to the industry.” Alejandro Expósito CEO

Click here to see how this process has taken years of research and improvements to help reduce costs and future problems in projects, always with the support of experts and laboratory studies.